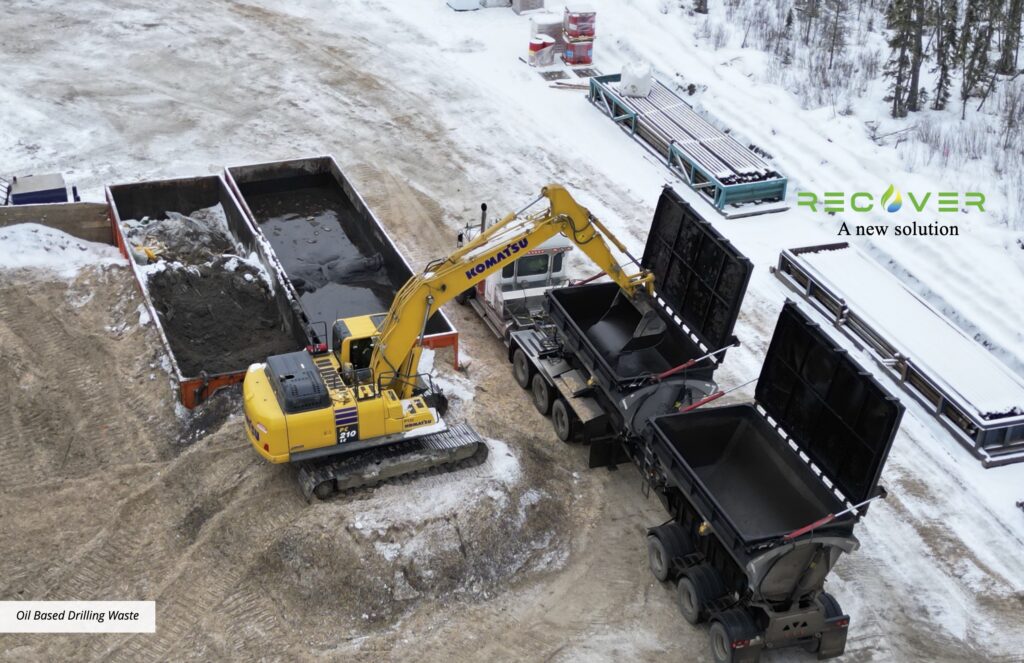
Click here to view the magazine.
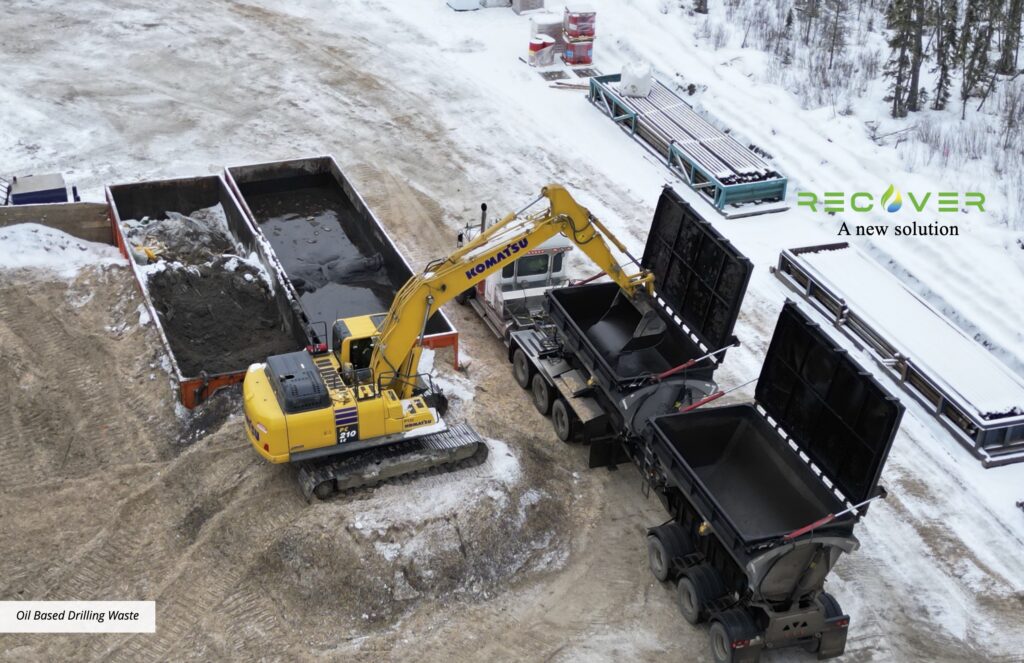
A new solution
Recover is a clean-tech waste-to-energy company that was formed with a mandate to solve the long term liability of oil-based drilling waste. The founding goal of the company was to provide energy operators with an environmentally sustainable solution that would allow oil-based waste to be cleaned and the recovered fuel to be reused in perpetuity. By providing that solution, their vision was to reduce landfilled waste, and thus eliminate the substantial volumes of greenhouses gases that would have been caused through the biodegradation of that waste.
After more than a decade of research and development, Recover succeeded in their mission – they came up with a now-patented technology that allows for industrial-scale recycling of diesel fuel. They have proven that technology in west-central Alberta, where they commissioned a first-of-its-kind commercial facility that is capable of washing oil-based drilling waste and creating a low carbon fuel.
“We created a remediation technology that functions like a recycling business,” says Stan Ross, CEO and president. “Now that we have proven that technology, we’re looking at expanding to other parts of the world, in particular the United States.”
Stan has personally been working in environmental technology for much of his career. Prior to forming Recover, he founded, grew, and then sold a successful waste-water treatment business. It was at the same time that he identified the longstanding liabilities associated with drilling waste. He committed himself to finding a solution, and after a period of research, bench-scale testing and field trials, he had a technology that was ready for commercial development. He created Recover in 2008, and roughly 10 years later the company commissioned that pilot facility in Alberta.
These days, Recover is backed by a dedicated team and a supportive Board of Directors, including former Prime Minister of Canada, Stephen Harper. In collaboration with that team, along with a roster of industry-leading suppliers – including Deloitte, the largest professional services network in the world, and Recover’s professional services partner of choice – Recover is well poised to launch a growth phase.
Proven technology
To understand the value and ground-breaking nature of Recover’s technology, first you have to understand what drilling waste is – as well as how pervasive drilling waste is.
Drilling waste is created every time a new, modern horizontal well is drilled. When an oil and gas company drills a well, pieces of rock are broke up by the drill bit and those need to be carried out of the well. A drilling mud is used to carry the rock particles to surface. Oil based drilling mud is used on nearly every modern oil or gas well drilled today. Oil base mud is mostly diesel fuel – in Canada, it’s known as base oil – and drilling mud provides operators with a number of inherent benefits like that of lubricity, wellbore stability and increased drilling speed.
The problem is that every piece of rock that comes out of the well is coated in the drilling fluid. Oil and gas companies then try their best to recover as much of the drilling fluid as possible because it’s expensive. However, due to technology limitations, much of the drilling fluid remains on the rock particles. In fact, as Stan explains, “there’s enough fluid on the waste that it behaves like a fluid, picture wet cement being poured for a sidewalk.”
“Therefore, the oil and gas company needs to dispose of what is now a toxic and fluidic waste, but it can’t be disposed of in an ordinary municipal landfill. Because oil base muds are primarily made from diesel fuel, the waste needs to be stabilized before it can go to an industrial landfill.”
But how abundant is this waste stream? According to Stan, “nearly every shale gas or shale oil well that is drilled in North America is using oil base muds in either the vertical or horizontal section, or both sections in many cases.” Those wells, he says, are producing anywhere between 200 tonnes to 1500 tonnes of oil based drilling waste, so “when you consider there are 10,000 wells drilled in a given year, you have millions of tonnes of drilling waste soaked in diesel.”
“What’s truly eye opening is every tonne of that waste contains one barrel of recoverable diesel. That means millions of barrels of diesel are going to landfill every year and as a commodity – and that diesel has an inherent value, if it can be recovered.”
Beyond the lost value, Stan also explains that diesel biodegrades in landfills and contributes significant volumes of greenhouse gasses. An independent study from ‘Life Cycle Associates’ has shown that every tonne of drilling waste contaminated with diesel produces approximately 1.5 tonnes of greenhouse gasses.
In the past, industry has invested heavily in solving this problem – Stan estimates that more than a billion dollars has been spent on research and development globally – but their default solution has been to manage the liability of diesel-soaked waste by mixing it with sawdust, or other stabilization materials and landfilling it.
“Incidentally, sawdust and other stabilization materials are added to create a material that’s bulky and stackable and doesn’t allow liquids to freely leach away,” Stan explains. “This is known as ‘stabilizing the waste’ so that it behaves less like wet cement and instead, more like peat moss.”
One of the early discoveries that Recover made, however, is that the solution resided in dedicated facilities that would have increased capacity when compared to on-site equipment. And for that to become economical, they realized, “the waste stream needed to be centralized.”
Recover’s technology is a solvent extraction process that is commonly used in many other applications including soybeans, canola oil, algae, palm oil extraction, and in analytical labs to measure constituents in sample matrices like contaminated soils. Recover has applied this process for washing drilling waste.
“The process is really simple to describe,” Stan says. “We wash the drilling waste with a solvent that dissolves the diesel fuel. We then recover our solvent using a distillation column. A distillation column is how a refinery produces diesel from crude oil feedstock. We then reuse our solvent in our process and we collect the tower bottoms – the recovered diesel fuel – and resell it. The cleaned solids are visually clean and those are sent to an industrial landfill for disposition. By removing the hydrocarbons, we reduce landfill volumes and avoid their subsequent biodegradation and resulting GHG emissions. That removes up to 2,500 metric tonnes of carbon dioxide equivalents per well.”
Recover came upon their solvent extraction process after years of reviewing all existing methods that had been tested in the past. After finding that they couldn’t enhance pre-existing machinery to be more effective, they experimented with over 50 surfactants, chemical additives and bioremediation techniques. A solvent called ‘hexane’ – a compound typically used to extract vegetable oils, such as canola – was identified as an extremely useful cleaning solvent and the company later discovered it was also useful in many commercial applications around the world.
Relative to thermal methods, Recover’s technology has numerous distinct advantages: it’s scalable and simple, it can produce a high quality recycled fuel, and it has a low capital and operating cost. On top of everything else, the tech is also now 100 per cent proven – since Q4 of 2021, the company’s first-of-its-kind facility in west-central Alberta has processed over 90,000 tonnes of drilling waste and produced over 15 million litres of distillate fuel.
Making an impact
For energy producers, Stan believes the value-add of Recover’s technology is obvious. They offer a solution that is better for the environment, reduces landfill volumes, and – most importantly – is practical to recycle, which Stan says makes it the “logical choice.”
He touches more on each of those points of difference:
“By recycling the hydrocarbons in the waste stream, we are avoiding substantive volumes of GHG emissions,” he explains. There’s up to 2,500 metric tonnes of avoidable GHG emissions per well and that’s a significant volume. Recover does that for operators on every well that recycles waste and for perspective, that’s equivalent to the emissions of 550 cars being taken off the road.”
“Another tangible benefit is that we are reducing landfill volumes by 50 per cent,” he continues. “We should always reduce waste and Recover removes the liquids and avoids the need for stabilization.”
“There’s also a ‘logical’ attribute. Energy is a commodity. We should never be landfilling an energy source. Recover’s technology can recover the fuel and recycle it. In fact, we have shipped our recovered diesel back to some of the same drilling rigs that sent drilling waste to our facility to be recycled. You have probably heard of a societal shift to achieve, wherever possible, a circular economy and some oil and gas operators are achieving that outcome by recycling an energy rich waste and only landfilling a waste with no residual value.”
In addition, while ‘being green’ has a reputation for being more expensive – particularly when establishing new technology – using Recover’s technology is actually cheaper for energy producers than simply landfilling.
“We don’t charge a processing fee,” Stan explains. “We are recovering a distillate fuel and diesel is valuable. We resell the fuel and the fuel pays for our processing service. Recover found a way to insert ourselves in the waste-to-value economic chain by providing our service at a cost point which is lower than what it costs to dump waste directly in a landfill.”
“We estimate that we save oil and gas companies about $10,000 per well by recycling. It costs more to landfill this waste.”
According to Stan, the obvious value-add that Recover represents has not gone unrecognized. Since debuting the technology, he says the public and industry reception has been “universally positive.” Locally, for example, he says Brazeau County has been very supportive of what they are doing and they have invited them to join a working group called the ‘Western Economic Corridor,’ which was established to help attract more clean tech companies to the area.
Stan also says that Recover has been “very fortunate” to work with the Business Development Bank of Canada, and they are currently working with other governmental organizations to help with their expansion plans. He partly credits that good fortune to the value people and government see in recycling in general. In today’s environment, he believes that “recycling has moved beyond socially acceptable to socially expected.”
“We’re providing energy companies with the ability to recycle and it’s an easy ask because landfilling less waste costs less,” Stan reiterates. “There are a few operators that still landfill because they think it’s easier, but we will continue to communicate our message that they need to reduce waste and stop landfilling energy. But there are also other companies that have been forward thinking and recycling waste has become their preferred operating practice.”
“At Recover, we are asking industry to take to work the same behaviours that they practice at home. The one nuance is at my home, I’m charged a fee to recycle whereas Recover actually results in a lower cost than landfilling waste. Today, recycling is easy to understand and the feedback we receive from the public is positive.”
Stan concedes, however, that there are a lot of companies operating or entering the waste-to-energy space. He describes what makes Recover different:
“‘Difference’ is usually a risk metric and everyone measures risk differently. Typically the top investor concerns are accessing waste feedstock, technology readiness, and bang for your buck – meaning, does your investment actually move the needle on emissions?”
“There are hundreds of waste-to-energy companies in the world that are competing for many waste streams. Some examples include biogenic waste, recycled plastics, used tires or spent engine oil. Because those waste streams are being sought by so many different parties, the waste or the “feedstock” has become commoditized. Recover doesn’t have a competitor in the traditional sense; we’re competing against a mindset of ‘landfilling is easy.’ Most in the industry view drilling waste as being at the very end, or bottom, of the value chain so they don’t see value in recycling. We’re changing that perception and accessing the waste.”
“We’re also different from our waste-to-energy peers with our technology progress. Few in the waste-to-energy space have an operating facility. Most are still at a pilot scale or building their first commercial facility. We are readying for a build program and we will be building duplicates of our current design.”
More than anything else, however, Stan believes the “most important differentiator” is the environmental impact their technology can make:
“Landfilling drilling waste unlocks the high carbon content of the waste because it manifests primarily as methane. Every well that recycles waste at Recover avoids up to 2,500 metric tons of GHG’s. So if the intent of your investment is to be green and be impactful, divide GHG avoidance by capital invested and Recover will beat out all players in the waste-to-energy space.”
A great story to tell
Recover is excited to expand into the United States – partly because they can produce about 45,000,000 litres (12mm gallons) of transportation diesel fuel at each of their expansion projects, and their diesel qualifies as a transportation fuel under the Inflation Reduction Act (IRA) in the United States.
“That program is very forward-looking in that the legislation isn’t prescriptive on the source of the feedstock; it’s prescriptive on providing a low carbon fuel,” Stan explains. “In other words, the IRA program doesn’t care where the feedstock comes from, so long as it produces a clean, low carbon fuel. That is a welcomed development for Recover and it helped solidify our direction to expand in the US.”
“We now have a strategic partnership with a waste management company that has assets in nearly every major shale basin and our next project is shovel-ready.”
It might be surprising that Recover’s diesel can be qualified as ‘low carbon,’ as they are recovering a fossil fuel, but Stan explains that they will be avoiding hundreds of thousands of tonnes of GHG emissions:
“Drilling waste contains hydrocarbons that biodegrade and turn into greenhouse gasses. Every tonne of drilling waste that biodegrades creates approximately 1.5 tonnes of greenhouse gasses. At just the first US project, we will avoid more than 350,000 tonnes of GHG emissions per year. That’s equivalent to avoiding the emissions from 70,000 cars per year and we can avoid that on every Recover project.”
“In fact, the carbon intensity of our transportation fuel is lower than that of most all other biofuels facilities being built in North America.”
Moving forward, the company is also excited about the future simply because of the positive narrative that has started being told about energy development. Stan credits that change in narrative to two things – the war in Ukraine, and the rising concern about energy supply.
“The war in Ukraine has taught the world that it matters where energy comes from. From a North American standpoint, this has really put local oil and natural gas resources to the forefront of future development.”
When it comes to concerns about energy supply, Stan believes that is a result of “the combination of underinvestment in fossil fuels” and “the challenges of the Energy Transition.”
“Today, people are more convinced that fossil fuels will be part of the energy mix for the foreseeable future,” he says. “We are being bombarded with messaging that we should be concerned with the emissions associated with energy development. So policy makers should be reflecting that in policy by finding ways to reduce those emissions. Now we’re finally seeing some political leaders are talking about decarbonisation instead of prohibition.”
As that talk intensifies, Stan says that Recover is well positioned as a company that can offer a solution. And when he takes stock of what they have already accomplished to date, he highlights the following:
“We are a waste-to-energy company that has a working commercial facility and we’re focused on a waste stream that is landfilled in abundance,” he says. “We have one of the ‘greenest’ technologies in the waste-to-energy peer group and supportive sponsors in Azimuth Capital Management, the Business Development Bank of Canada.’”
“We’re now well poised to launch a growth phase at Recover and that’s exactly what we’re going to do,” he concludes. “We have a great story to tell and we’re going to continue telling it.”
For more on Recover, their technology and how it works, their waste tracking and client services, and their latest news – and to get in touch with Stan and his team today – visit www.recover-energy.com