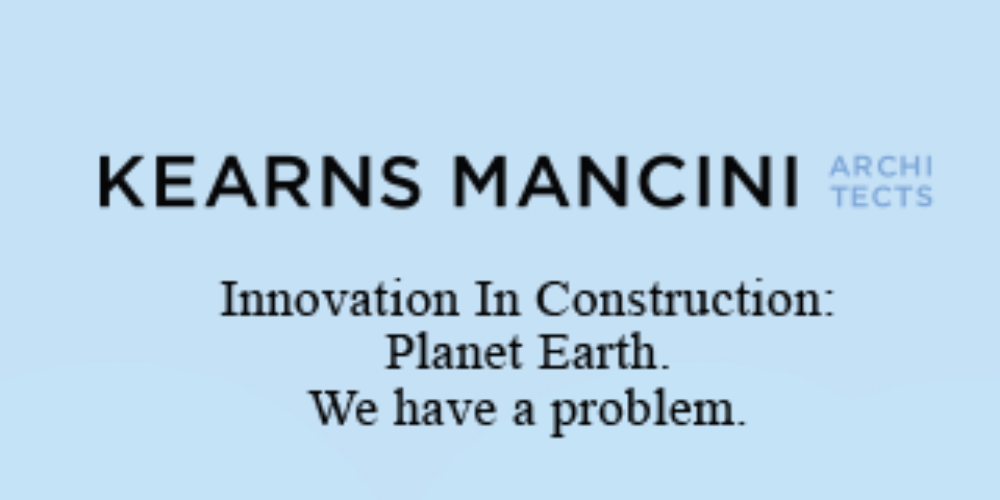
Innovation In Construction: Planet Earth. We have a problem.
You have heard it before. The way to ‘combat climate change’ is to innovate our way out of it.
We may want to innovate, but we don’t want to change. Not really.
Climate change communicators struggle with this all the time. Telling people that we
are facing an existential threat to human life on planet Earth is true, but it is not a winner. It does not motivate action; it doesn’t move the needle in the right direction.
The only way to motivate change is to show that through change our lives will get better. Things will improve. For each of us, personally. In the end, it’s just about us.
When it comes to housing, the challenge is even greater. Globally buildings are responsible for 40 per cent of carbon emissions. In Toronto, they contribute 57 per cent of the city’s greenhouse gas emissions – mostly from burning natural gas for heating. Transportation is the next big emitter at 36 per cent, with the majority generated by personal vehicles.
If we tackle buildings, we might have a chance. But how do we take on this massive challenge?
Construction is a conversative business. We’ve been building wood-frame homes and concrete offices and apartments the same way since the 1950’s and ‘60’s. So rather than change, we tinker. A heat pump here or there. Better windows. A few solar cells. This is what passes for innovation.
We need to design and build differently. The climate crisis forces us to think big, much bigger than we have so far. But we need a strategy that is doable now, with available skills and materials. And above all, a simple, affordable approach that makes things better for residents. Much better.
Enter Passive House.
“The Passive House offers so much,” says Deborah Byrne, COO of Kearns Mancini Architects (KMAI) and Director of Passive House Design, “health, comfort, climate resiliency, super energy efficiency, durable, COVID-resilient and so on. But equally in its simple architecture, in its owner type, in its materiality, it gives a sense that ‘anyone can build it.’”
How does Passive House help us meet our climate challenges and provide a better place to live?
Byrne cites the KMAI’s experience in designing and building the Putman Family YWCA – a 50-unit residence for women and women-led families with a community centre that offers support programs and education in Hamilton’s artistic Crown Point Neighbourhood.
“Designing using science,” she says, “to meet rigid functional requirements of Passive House ensures the building, if operated as designed, will use up to 80 per cent less thermal energy than a conventional building and will emit 36 per cent fewer GHGs.”
To build Passive House, you just must ‘think different.’ The Passive House Standard is the most rigorous building standard in the world.
“In most buildings, you design the shell, then you add the machinery. In Passive House, the building is the machine. It’s a puzzle, like playing with Lego to solve a Rubik’s cube,” says Deborah Byrne, who was recently recognized as one of the industry’s Clean 16, 2022 in the ‘Building: Design, Development & Management’ category.
KMAI is unique among architecture firms in that Passive House design is done in house. Most other firms ship it to another consultant, but they do not have KMAI’s experience and workflow process. “Once you learn Passive House, you just can’t unlearn it,” says Jonathan Kearns, CEO and Principal in Charge, KMAI, “It becomes the way you see every project, even if you are not seeking Passive House certification. You do everything you can to save energy and reduce the carbon footprint.”
“To build Passive House, the design team has to be truly integrated,” says Byrne, emphasizing the ‘truly.’ “You cannot design the building and then pass it on to a consultant to make it work. Every wire, every duct, every detail must be accounted for at the beginning of the design and every step of the way, or you will simply not meet the International Passive House standard.”
Passive House is a different way to design – a highly insulated, airtight building. It does not need the massive conventional heating and cooling mechanicals of a traditional build, rather it uses an energy recovery system that recycles the heat generated by the residents’ own bodies and their activities. “A hair dryer can heat a passive house,” says Kearns.
A passive house is also an active, breathable house. The energy recovery system provides dedicated fresh air ventilation in every room, allowing for higher-than-normal humidity levels of 40 – 50 per cent. Aerosolized particles are not transmitted in the more humid air; they drop to the ground. And the humidity maintains the body’s mucosa layer, protecting residents from airborne viruses.
This makes Passive House a pandemic-resilient environment that is perfectly suited for multi-unit dwellings, like long-term care homes where infection protection and control is paramount. The efficient control of the air and no air leaks allows these homes to maintain a constant flow of clean, fresh air and maintain the ideal relative humidity.
Innovation in building design requires different voices at the table. The Putman Family YWCA was designed by a women-led team for a women-led family residence.
Byrne was joined by Alice Gibson as project architect; Irene Rivera, an architectural designer; Natalie Krakovsky, architect; and Kelly Fisher, a Passive House consultant who helped develop the certifiable Passive House design. The YWCA Hamilton project is the first time she’s had a women-led design team, working for a women-led client.
Did having a women-led team contribute to the building’s innovation?
“We understand what women have to deal with, especially women on their own with children,” says Byrne, who says she’s incredibly proud of her team — most of whom are under 40.
“I think we can look at it from that perspective and be thoughtful in the design. We get it.”
There were also women on the engineering and construction side. For most of her career, Byrne says she’s been one of few women in the room — and women architects are often supporting male leaders.
“It’s unusual,” says Byrne. In her experience in the industry, “the leaders are usually men.”
But the industry is changing. The Ontario Association of Architects says it has about 28 per cent women — up from 23.7 per cent in 2015 — adding that nearly half their interns are women.
In Canada, the association says about 31 per cent of registered architects are women, according to data from the Canadian Architectural Licensing Authorities.
“While the process isn’t easy,” says Byrne, “it just requires patience and pride to meet the exacting standards and if anyone wants it, anyone can have it. We do want to inspire people to reach these targets. They just make sense for people, buildings, and the planet. By opening up about our path to achieve these high-performance targets, we hope that others will try it too.”
To meet the International Passive House Standard, the walls, and roofs of the Putman Family YWCA were R37.5 effective and R49 effective respectively and are thermal bridge free. By comparison, code buildings have significantly lower R values and permit some thermal bridging. Thermal bridging is the reason we have cold spots, condensation, and mould in buildings. Passive House insulations are approximately 50 per cent better than conventional.
To achieve design innovation, Kearns Mancini has had to achieve materials innovation.
The YWCA Hamilton wanted the Putman Family YWCA to be a concrete building and asked Kearns Mancini to work with a local precast manufacturer, Coreslab Structures. KMAI was up to the challenge; a precast Passive House had never been built before.
Coreslab Structures provided a Total Precast solution that incorporated a load bearing wall, continuous insulation, airtightness, and an exterior finish all in one component. The building consisted of over 330 precast components, including wall panels, beams, and columns and over 43,400 square feet of precast hollow core slabs.
Total Precast construction provided fast onsite installation, plant-controlled conditions for optimal execution, and helped eliminate the need for other trades on site. Overall, Total Precast reduced the entire project construction schedule and provided cost savings to the YWCA Hamilton.
“Coreslab has an insulated panel,” says Rick Sealey, KMAI’s on-site project manager, “so we worked with them to double their R-value. We used a European phenolic resin that hadn’t been used in Canada before, sandwiched between two slabs of concrete.”
Erecting 243 precast panels was a meticulous job that required the taping of every panel in place, like taping drywall. “We needed to tape the panels,” says Sealey, “to achieve the air-tight requirement of Passive House. This also happened with the massive three-pane windows which were 600 to 800 pounds, even a 1000 pounds each. They had to be moved in place with a robot sometimes to meet the tight tolerances.”
KMAI sourced a highly resilient sealing tape from Siga Swiss Canada for application at the Putman Family YWCA. Unlike conventional sealants, which are made from plastics, the company’s products are made from an acrylic polymer, a water-based material. Plastics used in building materials give off volatile organic compounds (VOCs), which are associated not only with poor air quality but degradation.
“With conventional tapes,” Byrne adds, “the sticky backing eventually breaks down and loses its grip, allowing heat to escape. Siga’s polymers, by contrast, are guaranteed to last for 50 years, which means they’ll continue to ensure air tightness – a key element of passive house.”
Traditional Canadian know-how was also essential. “The contractors are skilled at building hockey rinks, so they knew how to pour an insulated floor slab,” says Sealey, “We simply increased the R-value to meet International Passive House standards.”
Sealey’s constant and careful attention paid off. The Putman Family YWCA won an Ontario Concrete Award for its innovation. Most important, Byrne confirmed that the Passive House results were well below the required limits for the building to receive international certification. “It is all measured and modelled from the very beginning,” she says.
Throughout the entire process, from design to construction, the energy performance of the building was assessed.
Every aspect of the building design needed to have Passive House standards in mind with the materials used, orientation of the building and spaces, eliminating thermal bridging (conductive channels for heat to escape) and the energy-recovery mechanical systems. To eliminate thermal bridging, KMAI sourced an insulating fibreglass pin, rather than conductive steel, to hold concrete panels in place.
Further, aspects such as maximizing the south-facing windows to increase the heating of the building, minimizing north-facing windows to decrease heat loss, optimizing the surface area to volume ratio, continuous insulation of the Total Precast structure and having high performance triple-glazed windows all play a role to ensure the building performs as intended.
Kearns Mancini innovates on every Passive House project. They are responsible for what is currently Ontario’s largest Passive House complex under construction – Windsor Essex Community Housing Corporation’s new Affordable Passive House at 3100 Meadowbrook Lane.
Located amidst single family homes and other multi-unit residences in a Windsor neighbourhood, this 10-storey residential complex brings much-needed affordable housing to the City of Windsor. The 143,000 square foot building has 145 affordable housing units, as well as shared community spaces on each floor. The building creates a comfortable and healthy environment for all residents with a strong emphasis on creating community through vertical neighbourhoods.
“We worked on this project at the same time as the YWCA Hamilton,” says Deborah Byrne, “only here, rather than a modular concrete panel, a local manufacturer developed a modular steel wall system with us. They developed this completely to Passive House certification and it was the first certified wall component in Canada, Modpanel.”
All the pieces are in place to design and build Passive House in Canada. The innovation will continue, but Passive House, a concept first developed in Saskatchewan and then refined by a German physicist, looks like our way to innovate out of building’s massive contribution to the climate crisis.
Kearns Mancini has learned that building differently results in increased simplicity: a massively insulated, thermally broken airtight envelope; triple-glazed airtight, thermally broken windows; optimized orientation to catch southern solar energy; mechanical ventilation energy recovery; and optimized functional design.
“A Passive House design allows for the building to heat and cool itself most of the time,” says Jonathan Kearns, “providing significant occupant comfort for 90 percent less energy compared to conventional building methods. In a Passive House, you can sit next to a window in the dead of winter and not feel a draft, and then sit next to that same window at the height of summer and not feel overheated.”
For Kearns, not only is Passive House a better way to build, but it should also be the only way we are permitted to build. He should know. Kearns Mancini has been constantly innovating and collectively working on Passive House since 2009. They are Ontario’s leading Passive House architects.
“It is not a brand,” he says, “It is a building standard, balancing energy efficiency, occupant comfort, and affordability. The Passive House Standard should not be a privilege; it should be a right.”